内容
The process of making silicone products might seem complex, but it’s fascinating when broken down. Understanding the steps involved reveals why silicone is such a versatile material in industries ranging from electronics to healthcare.
Silicone products are manufactured through a series of processes, including mixing, molding, curing, and finishing, to transform raw silicone into durable and functional goods.
Let me guide you through the journey of how raw silicone is crafted into products that power industries and improve daily life.
[Table of Contents]
- How are silicone products manufactured?
- How many steps are there in the manufacturing of silicone?
- What are the raw materials of silicone?
- Who is the largest manufacturer of silicone?
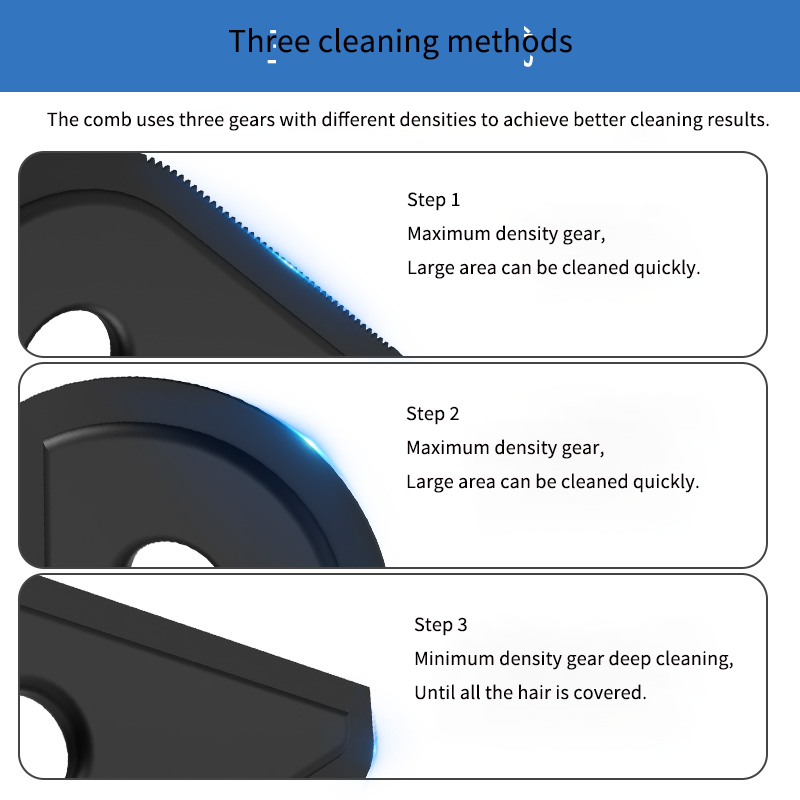
How are silicone products manufactured?
The manufacturing process of silicone products blends precision and innovation. Each step contributes to creating high-quality products with exceptional performance.
Silicone products are typically made through a process involving raw material preparation, molding or extrusion, vulcanization, and post-curing.
Dive Deeper: The Key Steps in Manufacturing Silicone Products
- Mixing and Compounding:
Raw silicone is mixed with fillers, pigments, and curing agents to achieve desired properties like strength, flexibility, and color. - Shaping through Molding or Extrusion:
- Molding: Liquid silicone is injected into molds to shape products like seals or medical devices.
- Extrusion: Silicone is pressed through a die to create continuous shapes like tubes or gaskets.
- Curing (Vulcanization):
High heat and pressure solidify the silicone, ensuring it maintains its form and properties. - Post-Curing and Finishing:
Products are heated again to enhance their durability and then trimmed or polished for a smooth finish.
Silicone’s unique properties, such as resistance to heat and chemicals, make this process essential for creating reliable, long-lasting products.
How many steps are there in the manufacturing of silicone?
The process of manufacturing silicone can vary based on the product, but the steps are well-defined and precise.
Generally, silicone manufacturing includes four major steps: raw material preparation, shaping, curing, and finishing.
Dive Deeper: Why These Steps Are Crucial
- Step 1: Preparation of Raw Material
Silica is processed into silicone by combining it with other chemicals like methyl chloride. The result is silicone polymers that are the foundation of silicone products. - Step 2: Shaping
Depending on the product, shaping is done through injection molding, compression molding, or extrusion. - Step 3: Curing
Vulcanization transforms silicone from a soft material into a strong, elastic product using heat and pressure. - Step 4: Post-Processing
This step ensures the product meets quality standards through testing, trimming, and surface treatment.
Each step ensures the material maintains its versatile and durable properties. Skipping or rushing any of these steps can compromise the product’s performance.
What are the raw materials of silicone?
Raw materials play a vital role in determining the quality of silicone products. The foundation of silicone begins with materials that are abundant and sustainable.
Silicone is primarily made from silica (sand) combined with methyl chloride and other chemical additives to create silicone polymers.
Dive Deeper: The Core Ingredients
- Silica (SiO2):
The primary component, silica, is derived from quartz sand. It provides the essential silicon needed for silicone synthesis. - Methyl Chloride:
This chemical reacts with silica to form a silane, which is then processed into silicone. - Catalysts and Additives:
These include curing agents, pigments, and fillers to enhance specific properties like strength, elasticity, or thermal resistance.
Here’s a quick table summarizing these raw materials:
Raw Material | Purpose | Source |
---|---|---|
Silica (SiO2) | Base material for silicone | Quartz sand |
Methyl Chloride | Reactant for silicon compounds | Chemical plants |
Additives | Enhances properties | Varies |
These materials are carefully combined and refined to create the versatile silicone products we rely on today.
Who is the largest manufacturer of silicone?
Silicone manufacturing is dominated by global companies known for their innovation and scale. But who holds the top spot?
Dow Inc., based in the United States, is widely recognized as one of the largest silicone manufacturers globally.
Dive Deeper: Leading Silicone Manufacturers
- Dow Inc.
A pioneer in silicone technology, Dow offers products for industries like automotive, healthcare, and electronics. - Wacker Chemie
This German company specializes in high-performance silicone materials used in construction and consumer goods. - Momentive Performance Materials
Known for its advanced silicone solutions, Momentive serves industries like aerospace and energy.
Why Are These Companies Leaders?
- Innovative R&D: Constant innovation to improve silicone properties.
- Global Reach: Large-scale manufacturing facilities and distribution networks.
- Industry Specialization: Focus on diverse industries, ensuring tailored solutions.
These companies set the benchmark for quality, ensuring that silicone remains a vital material across industries.
結論
The manufacturing of silicone products involves precise steps, from raw materials to finishing. By understanding this process, we can appreciate the effort that goes into creating such versatile, durable, and essential materials.
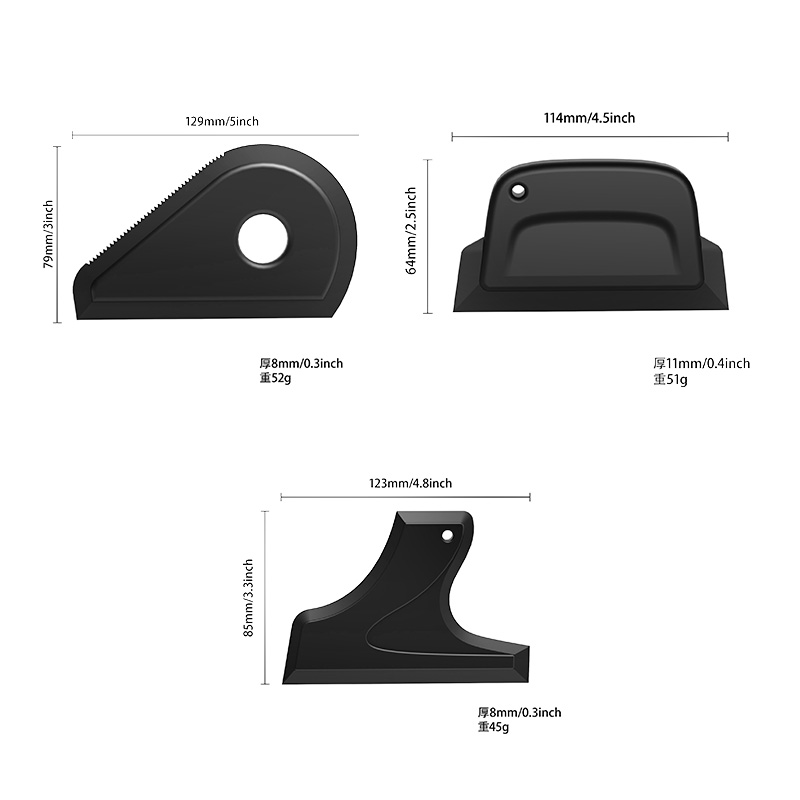